Odyssey Academy: Streamlining Rework Shop Orders for Improved Efficiency
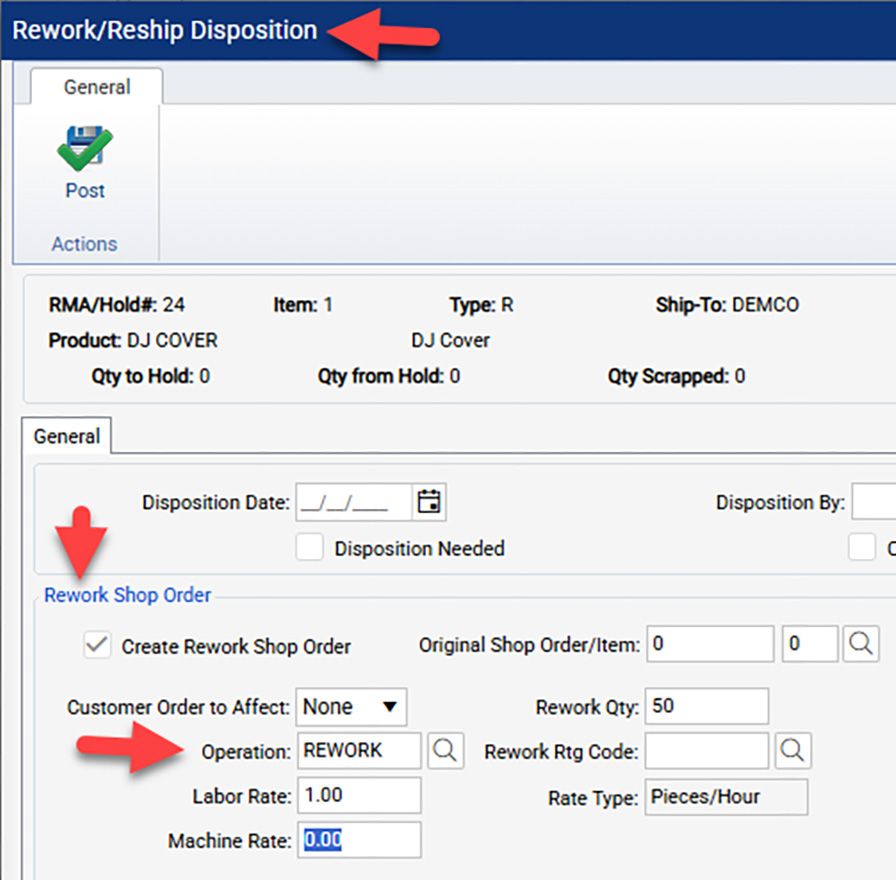
In manufacturing, maintaining high-quality standards is paramount. However, even the most stringent of quality control measures can't eliminate the occasional necessity for rework. Rework shop orders come into play when a product doesn't meet the required quality standards and needs corrections. Let's delve into the mechanisms and benefits of rework shop orders. There are two types of Rework Shop Orders. One used with a predefined rework routing the second used with an operation called Rework.
Understanding Rework Routings
Rework often involves multiple operations— more than just a simple touch-up. This complexity necessitates a structured approach, commonly facilitated by rework routings. Rework routings allow differentiation between regular and rework operations, ensuring that non-standard sequences are followed for rework tasks. For instance, instead of the standard sequence 10-mold, 20-grind, 30-polish, and 40-inspect, you might see 925-regrind and 935-repolish for rework tasks. This strategy not only distinguishes rework operations but also streamlines the process.
The Role of Rework Shop Orders with a Rework Routing
A rework shop order is integral in executing rework routings effectively. When a rework shop order is created, appropriate rework operations are automatically assigned based on predefined routings with unique non-standard sequences. This automatic creation ensures that the rework scheduling aligns with these sequences, thereby maintaining a clear delineation from standard production processes.
Creating a rework shop order triggers specific action:
- Sequencing and Scheduling: The specific rework sequence is applied, and operations are scheduled accordingly.
- Cost Management: The associated costs of rework operations are categorized as non-standard, thus simplifying job costing and financial tracking.
- Inventory Management: Parts under rework are held at specified points in the routing, ensuring they are not confused with standard production inventory.
The Role of Rework Shop Orders with a Rework Operation.
A Rework Operation is one that can be used when not using a Rework Routing. Not all products need to have a predefined Rework Routing but there could be a need to do Rework on the product. This can be based on the Internal Hold or Customer Return processing steps. These process steps can be reviewed in the Odyssey Help Text under Holds and Returns Tracking Scope.
Operational and Financial Benefits
Rework shop orders offer several operational and financial benefits:
- Improved Traceability: By clearly distinguishing between standard and rework operations, it becomes easier to track the progress and effectiveness of rework processes.
- Enhanced Scheduling: Using non-standard sequences helps with better scheduling and managing rework operations without disrupting the regular production flow.
- Cost Efficiency: Accurate cost tracking ensures that rework expenses are accounted for separately, aiding in overall financial management and budgeting.
In conclusion, while rework is an inevitable aspect of manufacturing, leveraging structured rework routings/rework operation and dedicated rework shop orders can significantly enhance efficiency and ensure that quality standards are upheld consistently. By adopting these practices, manufacturers can better manage rework processes, leading to improved product quality and customer satisfaction.
For more in-depth insights, feel free to reach out to our support team or visit our resource center for detailed guidelines and documentation.
< Back to Blog